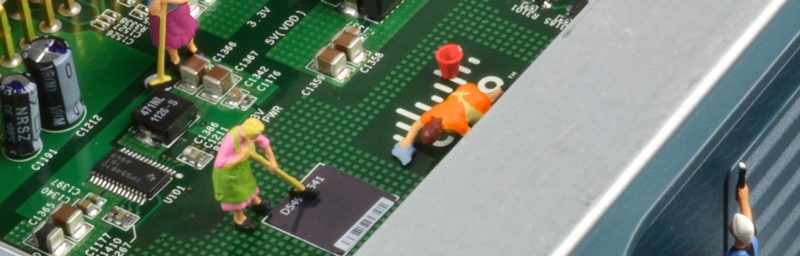
7. Have kit ready for plug and play
Ship ready for 'plug and play'
We've all heard it, or something very like it, a hundred times. "What time will you be home? The kids have forgotten what you look like." Anyone working with networks is familiar with long and unpredictable hours - in part because, let's be honest, we're all pretty much hooked on what we do.
What we do is fun. At least, it's fun when you can log in and out, engage and disengage, when you want to. It's less fun when you have to revisit work that's been done before and shouldn't need to be redone. For my part, I'd much rather be home reading my son "Slinky Malinky" than rehashing work that really should have been put to bed already. Life's too short.
Life is too short, and on top of that, the economy is too unforgiving. Time, as has been noted so often, is money. Your engineers' time is no different to anyone else's in this respect, and wasting it is a direct cost to your business. In the current economic climate, with growth and even survival depending so heavily on cash flow and profit, that cost could make the difference between staying afloat and going to the wall. Making cost savings without impacting quality is a key priority.
Build, configure and test
Let's look at a common scenario. A customer's network installation is just around the corner - you're waiting for delivery of the network devices and associated items. Engineering resources have been planned and allocated. The customer is champing at the bit and the pressure is on.
What happens next? You receive the equipment, unpack, build, configure and soak test it. A couple of days later, you dismantle it, pack it up again and ship it off to the customer.
A simple question
At this point, I'd like to ask a very simple question. Why do it this way? On receiving the equipment the customer or your installation engineer will unpack, build, install, configure and test it. There is more than a little duplication of effort going on here. There's increased risk of damage, and time and money are being wasted.
Avoiding this risk and waste is actually very easy. While awaiting delivery of the network devices, memory, cables and software, call the customer and ask them if they would like the equipment supplied with their configuration pre-loaded, with any necessary memory and software upgrades made. In short, would they like it delivered ready for plug and play installation? I can almost guarantee that most will give you an emphatic "Yes please".
Make life easier
This will make the customer's life easier, of course, but it will also make your life easier and save you time and money. Keeping the equipment in your testing station until the memory and software has arrived, and then making the necessary upgrades there and then will mean the job is done and the equipment can be shipped to the customer ready to run, with a test report certifying the upgrades that have been made.
As well as saving you time and money, this approach avoids the situation in which the customer discovers that a device has insufficient memory for the required software image. It also means that the customer gets network equipment that has been tested as they will use it - and that's the test that really matters.
Investing this small amount of additional effort before shipping the equipment to the customer can save your installation engineers hours of on-site time. That means savings in engineering costs, improved customer satisfaction, fewer network teething troubles, and, of course, that you and your engineers get to remind yourselves of what your family look like. That's what I call a result.